1. Hole arrangement
The arrangement of sieve holes includes horizontal and vertical holes, both of which are equilateral triangles. The screen with horizontal holes is that the direction of material running is perpendicular to one side of the triangle. The vertical hole is that the running direction of the material is parallel to one side of the triangle. When selecting a screen with a large aperture (aperture>Φ4.0), the way of arranging the holes has no effect on the production capacity. Due to the high production capacity and the impact of the material on the screen, it is easy to choose a screen with vertical holes.
The vertical interval between the two holes just forms a strong support for the screen. When selecting a screen with a small aperture (aperture ≤Φ4.0), the decrease in the overall production capacity of the material also reduces the impact force on the screen. Therefore, a horizontal row of holes with no material incident blind area should be used. Practice has proved that when using small-diameter sieves, under the condition of the same opening ratio and the same thickness, the production capacity of the sieves with horizontal holes is 5%-10% higher than that of the sieves with vertical holes.
2. Sieve aperture ratio
When selecting sieves, give priority to meeting the requirements of product particle size, and then select sieves with high density and large aperture as much as possible according to the strength that the sieves can withstand. The relationship between the sieve hole diameter and the crushing particle size is generally: the strength of the finished product ≈ (1/4-1∕3) the sieve hole diameter. At the request of Liuhe Xinlong, we have achieved an opening rate of 45% for the Φ2.0 screen. The problem is that the opening ratio of the screen is increased, and the powder output efficiency is also improved, but the impact value of the screen is decreased. The cleaning of raw materials cannot be absolutely clean, and some larger sand and gravel can easily break the sieve, resulting in return material, which increases the production cost. So you can come to see the
feed crusher machines.
After several tests, on the basis of ensuring the original 42% high opening rate, the aperture on the back side of the screen was increased while the aperture on the front side of the screen remained unchanged. A kind of guide hole similar to ring die is formed. Use with the burr side facing the rotor. Because in the direction of the material flow, when the material passes through the screen hole, it collides with the edges and corners of the burr surface, which can play the role of friction and crushing, and can increase the screening capacity. At this time, the bell mouth increases the material feeding inclination, which just plays a role similar to the material guide hole of the ring die, and the crushing efficiency is significantly improved compared with the original screen.
3.Installation of screen
When the sieve is installed, the sieve with the required aperture of the material particle size is installed on the front side, and the sieve with a larger size is installed on the back side, which can not only meet the particle size requirements of the material but also improve the crushing efficiency. When the sieve is punched, microscopic dents will be formed on the positive side, the circumference of the sieve hole will become smooth and dull, and the cutting ratio will decrease. If the screen is installed with the anti-burr facing outward, it will also cause the material hanging at the burr to block the screen hole, which will affect the powder output efficiency.
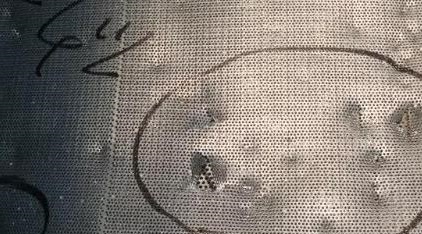
4. Failure of the screen
Most of the damage to the screen is caused by foreign objects entering the crushing chamber. Small holes can be reused after repairing by welding. When there are many holes, the effective screen area of the repaired screen is greatly reduced, and then repaired. Use will lose the use value, only to replace the new screen.
When comet craters appear in the sieve hole, the cutting speed will be slower than that of dropping the powder. Even if there is no foreign matter, the sieve should be replaced. If it is used again, the wasted power consumption will far exceed the residual value of the sieve.。
5. Influence of temperature rise on production capacity during pulverization
The front-line employees who know crushing may have encountered such a phenomenon. When the crusher first started to work, the crushing speed was very fast. After working for one or two hours, the crushing speed has a slow downward trend. This phenomenon is more obvious especially when making small-aperture sieves for pig feed and fish feed. After the crusher is reversed, the production capacity returns to a state of high production capacity. That is because, after the pulverizer works for a period of time, the heat generated by the hammer hitting the material and the heat generated by the friction of the material colliding with the screen will cause the temperature of the pulverizing chamber to rise.
When the sieve is in such a harsh environment for a long time, the fatigue strength, surface hardness and cutting force decrease, which directly leads to a decrease in the powder yield. It is best to stop feeding at this point and let the grinder run idly for a few minutes. In a few minutes, under the action of negative pressure, the temperature of the crushing chamber can be lowered and the production capacity can be restored.